生产制造型企业通常拥有较多的生产设备和较大的厂房面积,在生产运营过程中伴随有较大的能源消耗,因此具有较高的管理难度,易形成巨大的隐患,造成巨额的经济损失,需要相应的信息化系统来进行管理
泰坦工业数字化平台
(已接入DeepSeek)
可对生产设备进行全生命周期的智能化管理,实时监测工作状态,及时识别隐患,避免重大部件/设备/产线的经济损失
可对厂区内各种机电设备和系统等进行综合管控,有效降低人工管理难度,优化管理颗粒度,提升管理水平
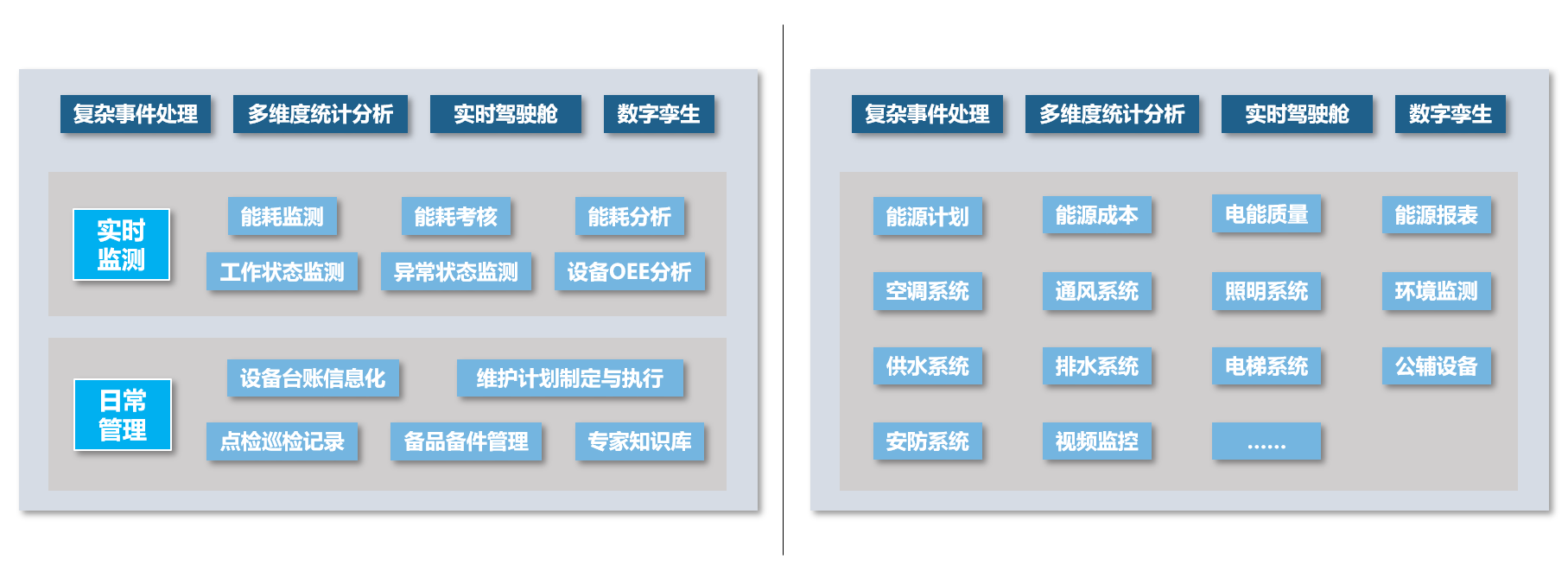
基于“云-管-边-端”的典型架构
通过物联网、大数据、数字孪生等技术,实时掌握设备生产运行的状态与能耗,在PC端和APP端通过大屏驾驶舱、3D数字孪生等形式展示出来,并提供多维度分析报表供管理人员决策
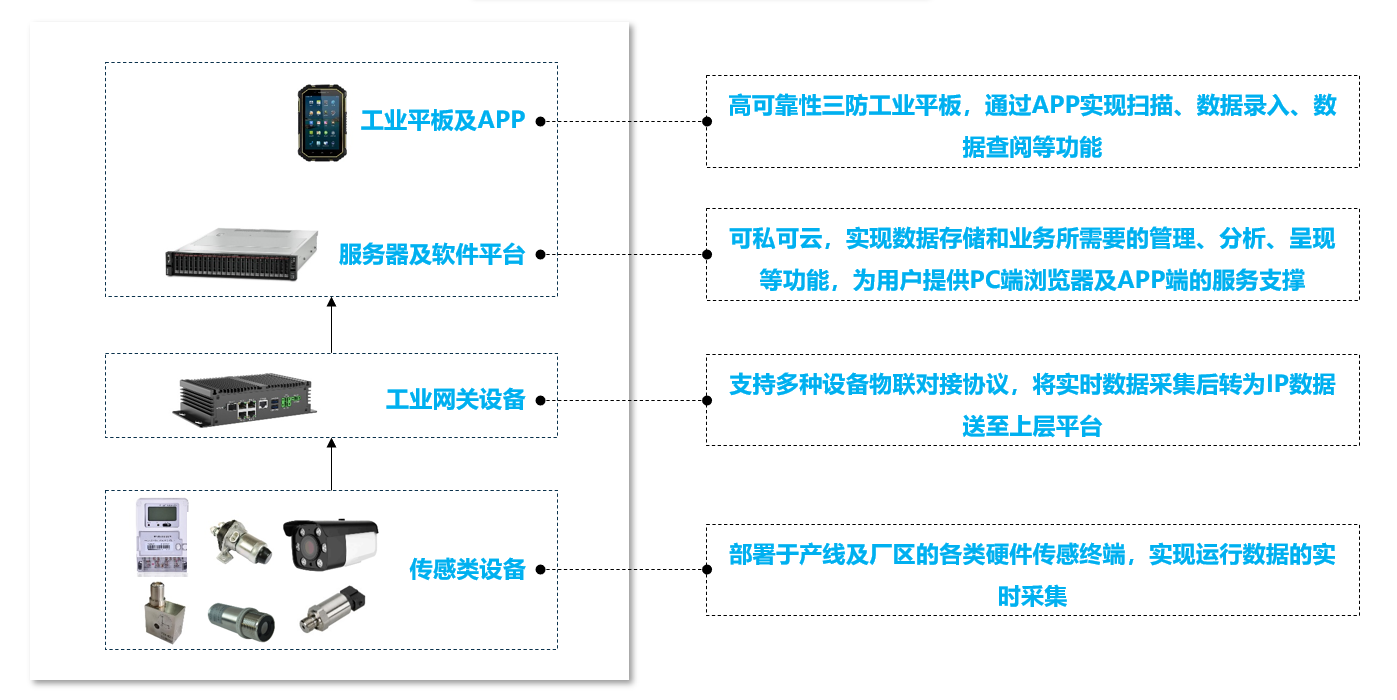
分层次的逻辑架构
通过层次分明的架构体系,分层封装实现各类功能,从而满足各类场景定制化需求
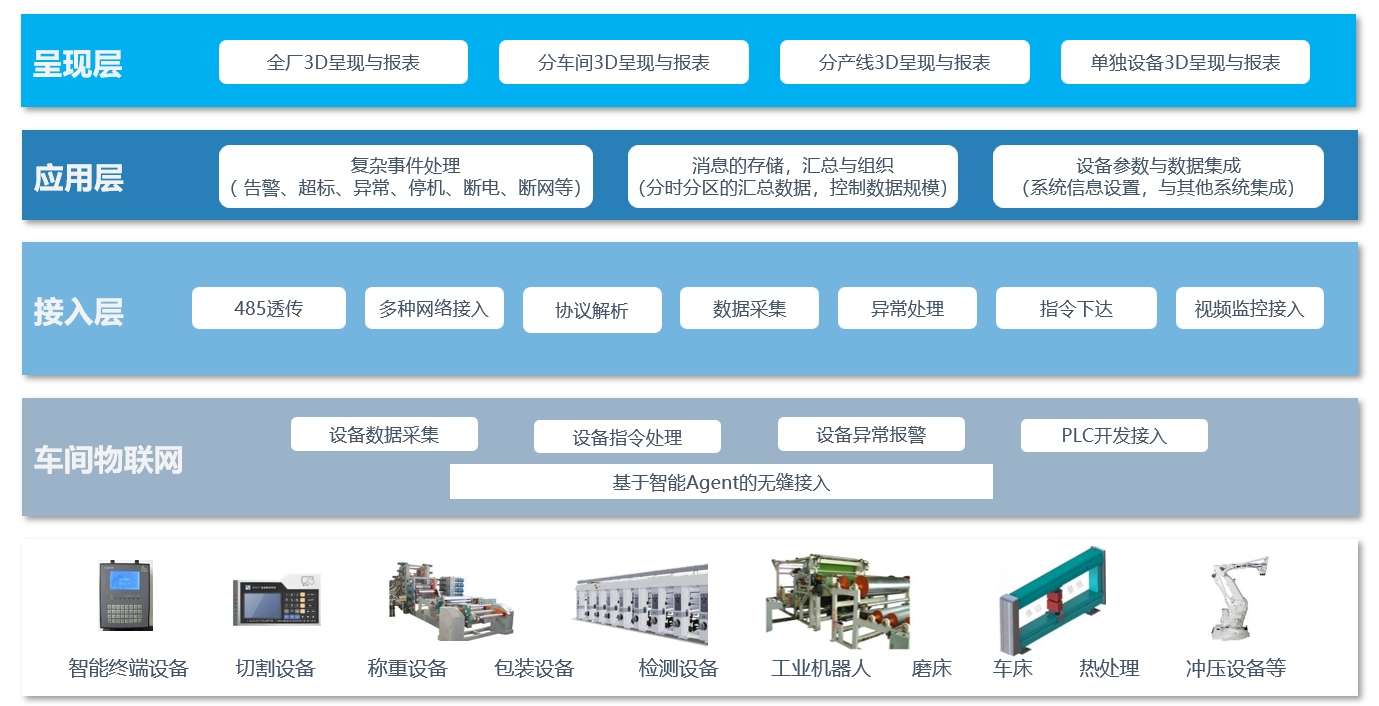
系统部署示意图
工业物联网+IP网络(内网/互联网),实现随时随地的远程监控与管理!
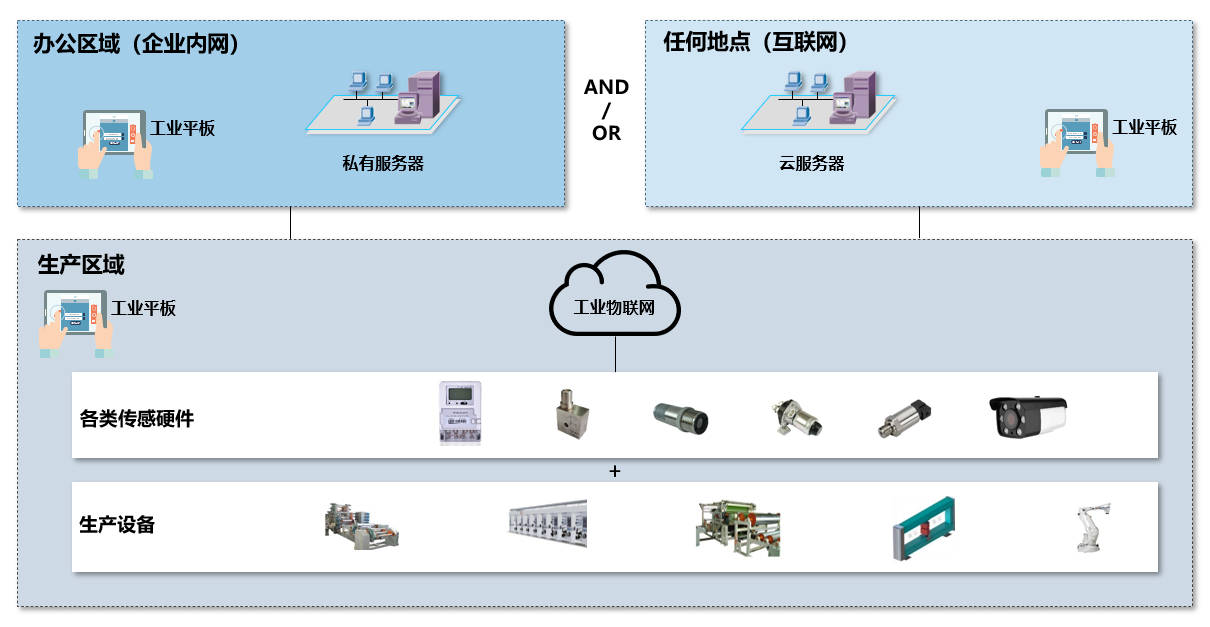
参考界面一:事件引擎与多维度能耗绩效管理
使用流数据处理引擎,可快速识别设备三态,并接入更多规则,实现复杂事件的处理能力。能耗绩效管理可关联到车间、班组等不同级别,下达用电优化指标,进行用电精细化管理
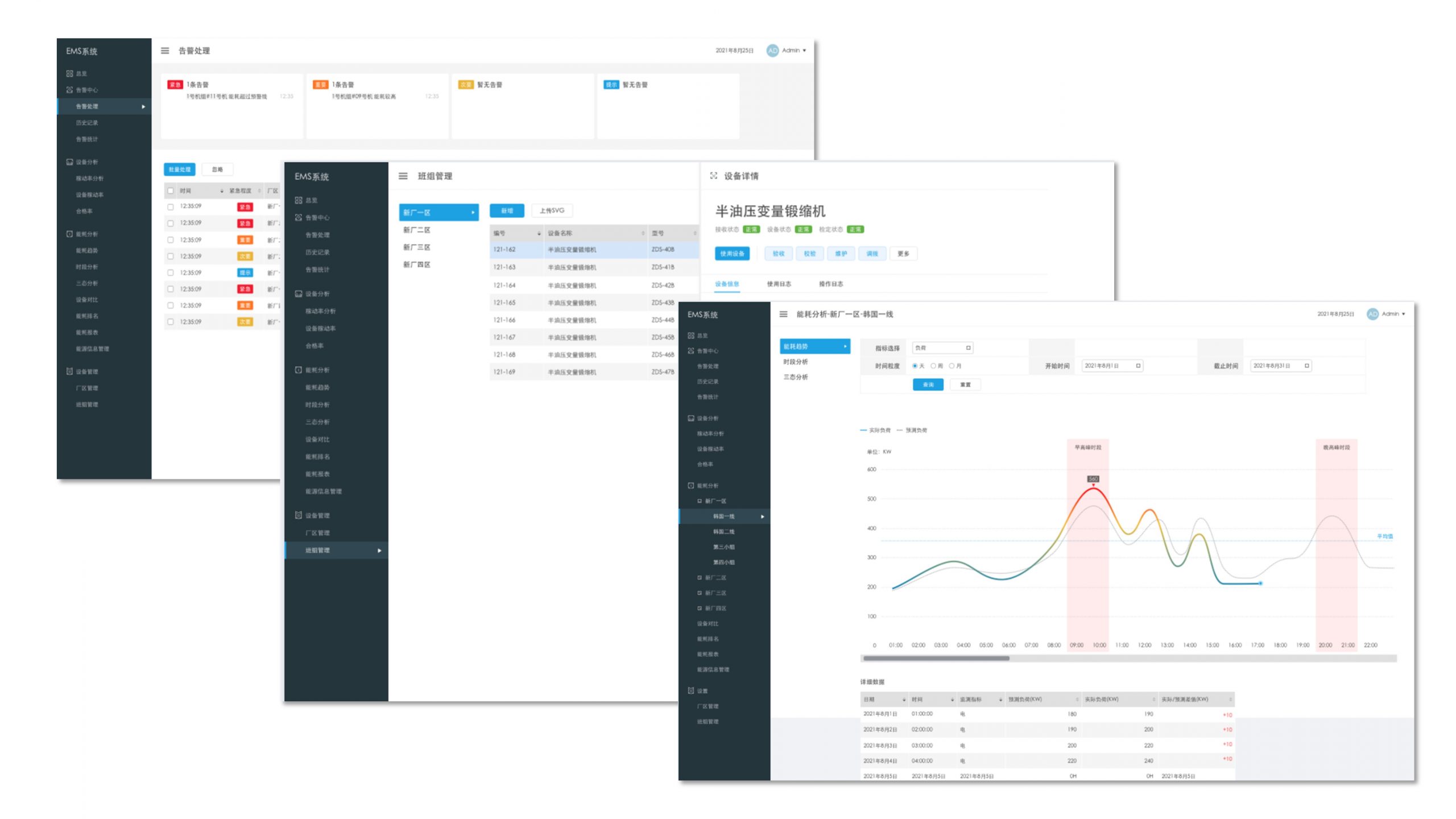
参考界面二:设备使用情况与分析
通过对设备电流数据的监控管理,可以发现非常多的有价值信息,对生产工作中的管理力的提升有巨大的帮助。如:技术工人在操设备过程中的不良习惯、离开空转、频警开关机等
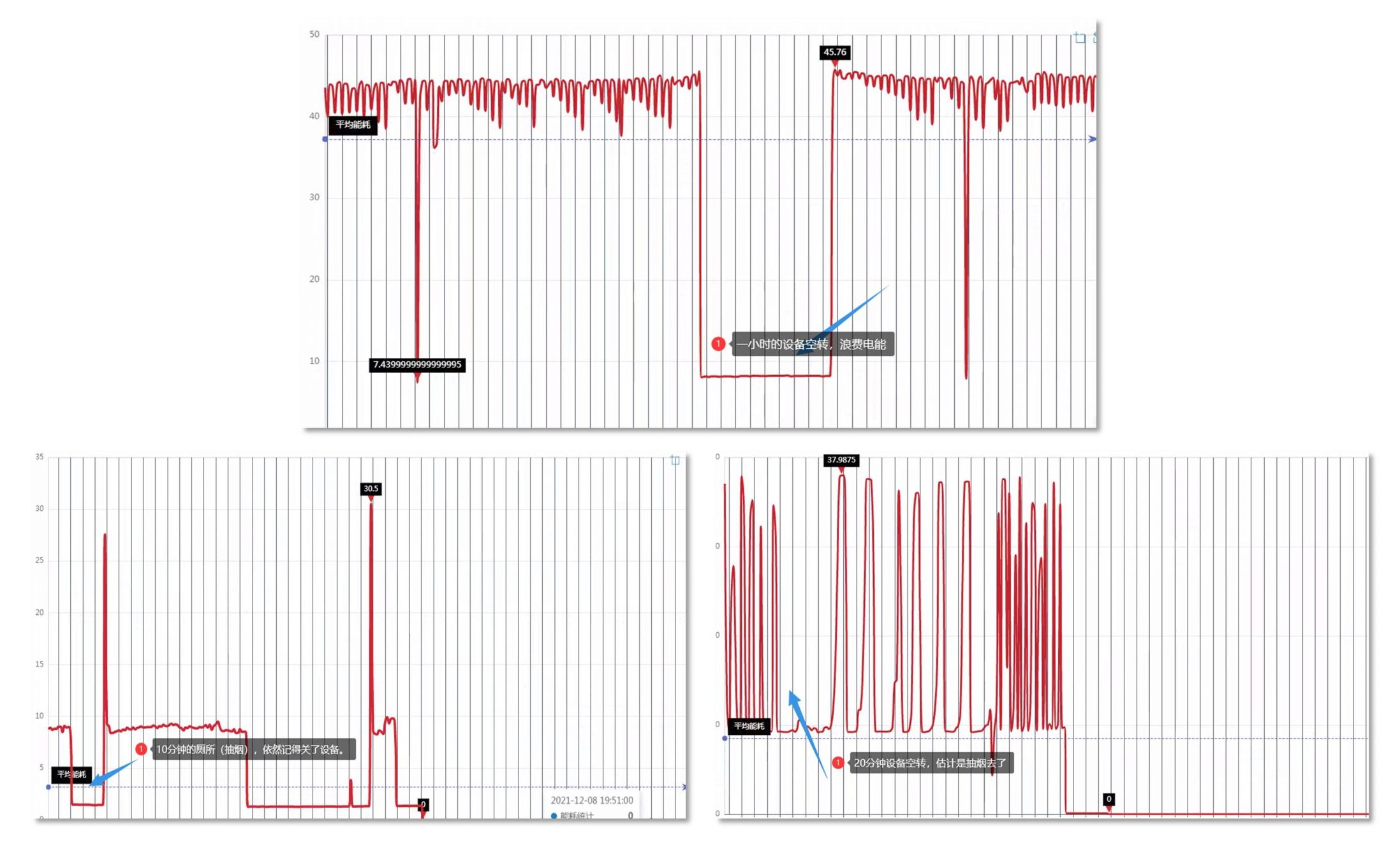
参考界面三:设备三态识别与分析
使用物联网大数据分析,可自动识别设备的状态,通过高精度统计得知设备的真实运转情况
设备的阈值(开机,关机,空转,异常等)可通过高阶算法自动识别,无论设备是否带了什么附属设备(取暖设备、风扇、冷却设备等),或者加工特定的产品,导致电流阈值的变化,算法都能动态修正其值,计算出设备的真实状态
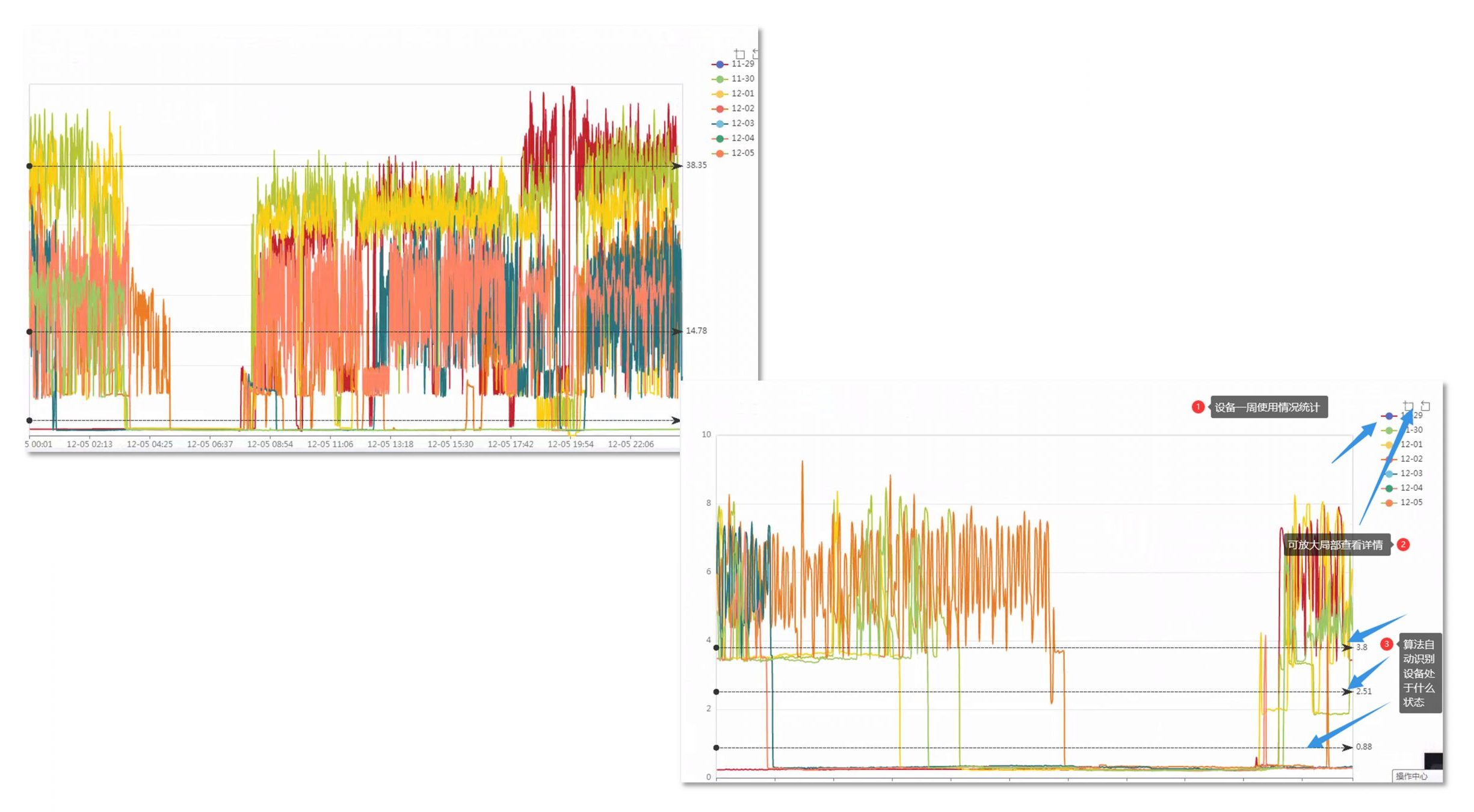
参考界面四:基于数字孪生的3D呈现
可分别于设备、产线、车间、厂区等级别对实际物理模型进行数字孪生3D建模,并将实际参数映射到虚拟空间,使系统能够更加实时、直观、真实地展现当前状态
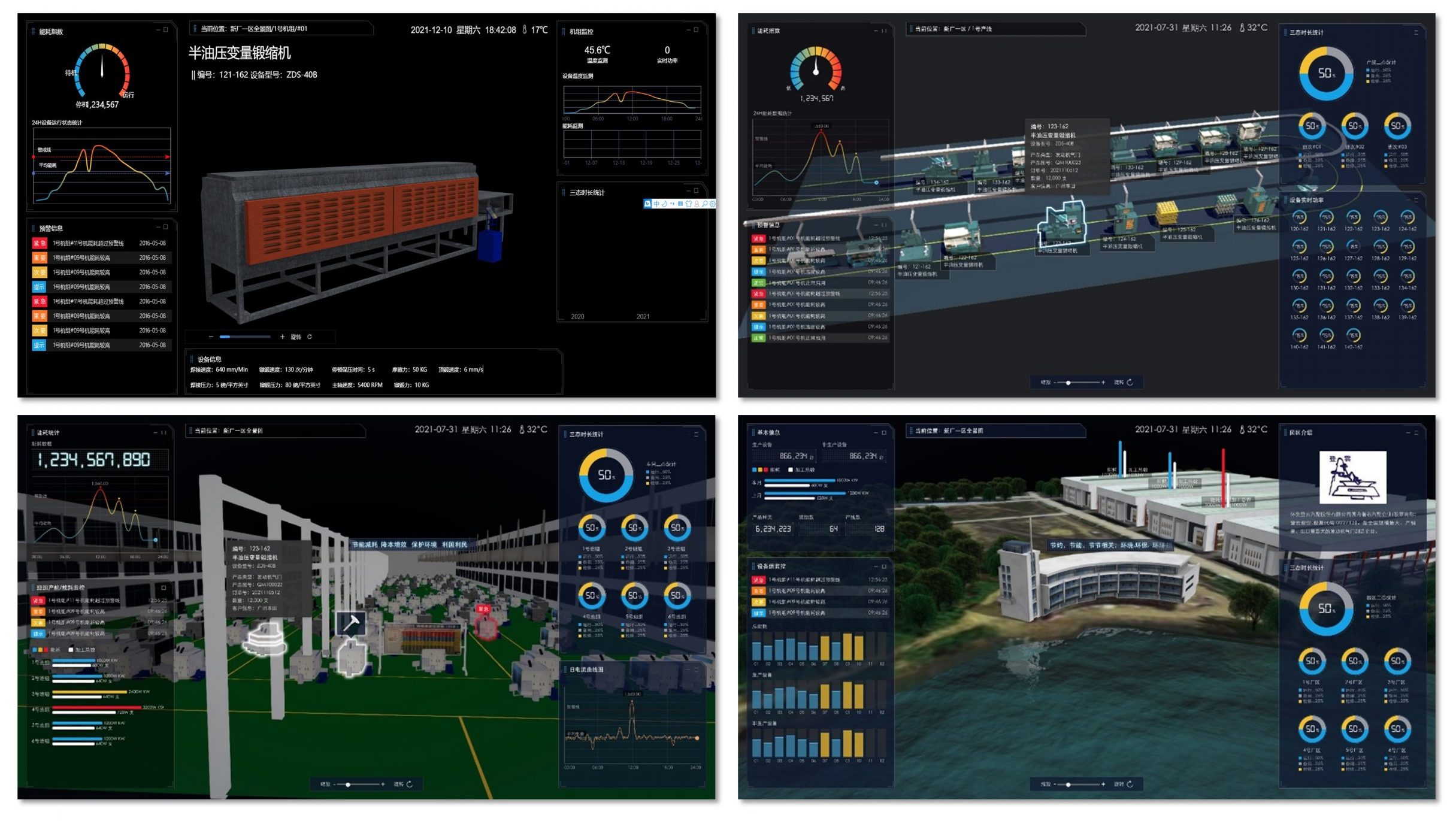
马上联系!
电话/微信:136 8689 1247(赵先生)